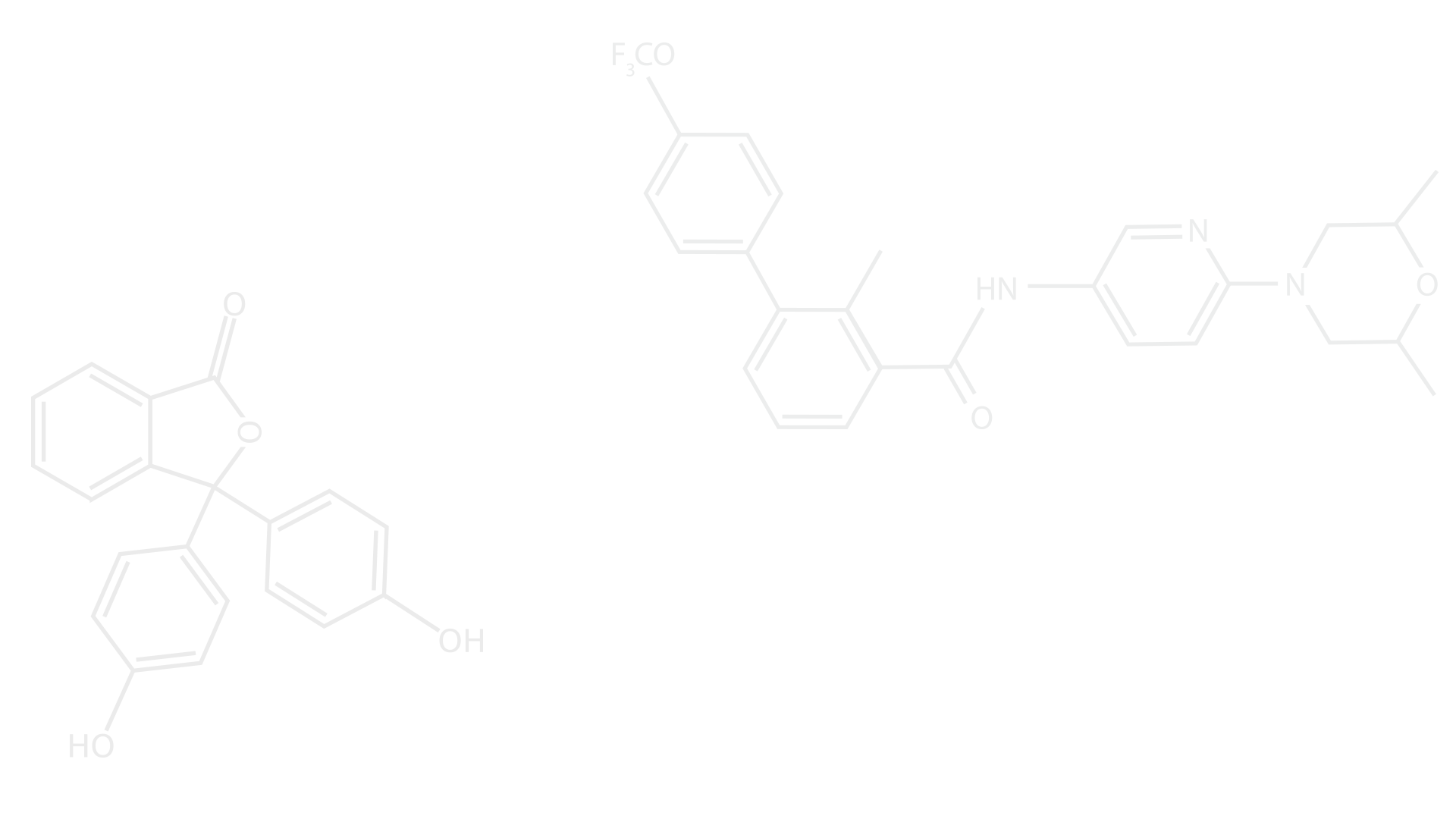
Testing
The purpose of testing is to ensure that the device meets the design requirements and predictions. These tests will be conducted in a similar manner as the full scale project would be, testing the downriggers ability to withhold the force that will be created by the vertical member during the leveling process. Based on the calculations made during the fall quarter for the full scale project, certain equations made on the ‘green sheets’ will be reverse engineered, using the new dimensions for the proof of concept model to arrive at usable and testable numbers for the this section.
Method/Approach:
The first test applied to the part will be a fitment. This will account for any variances within the metal or the welded guides. This test will prove that both parts fit together and there is enough room for the inside beam to move freely without any major restrictions, but also to provide enough rigidity so that following tests can be accomplished.
The second test is a static analysis of weight on one end, and will provide a visual display that the beam is capable of holding the predicted load at the designated extension length. This test will incorporate a large C-clamp, along with two volunteers balanced the end of the inside beam whilst extended. The largest amount of force created when the beam is loaded with weight at the designated extension length is located at the opposite end of the inside beam from where the weight is positioned. This end of the beam will be weighed down with a combination of weights and people.
The third test will be an analysis of the spring used for the retraction process. This will test against how much force is needed to keep the articulating arm at its designated extension length, and also how much force is needed to fully extend the enclosed beam. After one round of testing the force needed to extend the device and keep it extended while it is dry, a round of testing will be conducted after a lubricated application is applied to the inside and outside beam parts.
For the load test weight will be added to the beam while at its extended length until the projected figure has been reached including a safety factor, which means that the final result will be under the max load so to avoid yielding or any other irreversible damage.
​
Test Procedure:
All tests will be conducted inside of the Washington Society for Safety Engineers classroom at the Central Washington University. All testing completed is non-destructive and no personal protective equipment is needed. All test data will be recorded onto green sheets and provided below.
Assembly/Fitment
This test will be performed to guarantee that all parts fit together. Test duration should last no longer than 5 minutes
Steps:
-
Gather all necessary project parts (small diameter beam, large diameter beam, steel braided cable)
-
Lay beam on flat table, so that the long edge is laying down
a) The welded guides in figure one labeled "4" should be closest to the table surface
-
Insert the back of the small beam concentrically into the front of the large steel beam.
a) Make sure that the welded guides on the larger steel beam as well as the small steel beam (labeled "4" in both figures) are oriented so that they are closest to the table surface. Simply slide one beam into the other so that the larger beam completely encloses the smaller beam
a) Make sure that when the beams are fully enclosed, the guides on the outside of the small steel beam are on the opposite end of the assembly as the guides on the inside of the large beam
-
Thread the provided steel cable through the opening at the front of the large beam (label "2", large beam)
-
Route the steel through the inside of the space provided between the two beams toward the back of the small beam to the welded stock (label "3", small beam). Thread the cable through the opening at the back of the small beam (label "1/2", small beam)
-
Wrap the steel cable around the welded stock located at the back of the small beam (Label "3", small beam) and return the cable through the openings at the back of the steel beam and return it to the front of the opening at the front of the large beam (label "3")
-
Wrap the steel cable around the pinned rollers (large beam, label "1/3" and lay the cable pointing towards the back of the large beam
-
A successful test will result in being able to move the enclosed beam into the larger beam with little opposition from the metal to metal contact or the steel cable.
-
Record time to complete test. Record a pass or fail.
Weight/Load test
This test will show that the beam assembly is capable of supporting the predicted amount of weight. Test duration should last no longer than 5 minutes.
Steps:
-
Gather all supplies necessary for testing (concentrically oriented steel beams, 450 pounds of weight in lead and human volunteers, ruler, marker)
-
Measure exactly where the middle length of the inside beam is. This point should be exactly 1.5 feet. Mark the small beam for future reference
-
Lay the beams down on a table in a similar manner to the fitment test, steps II and III.
-
Using a large C-clamp, secure the outer beam to a flat table, making sure that the end of the outside beam is not protruding from the table.
-
Assemble the beams together in a similar concentric fashion as the assembly/fitment test steps II and III
-
Using the mark from step II of this test, extend the front of the inner beam out of the front of the outer beam to the 1.5 foot mark. For this test the spring operated retraction device should not be attached.
-
Because 450 pounds of weight proved to be too difficult to secure to the end of the beam, several volunteers are asked to balance themselves on the end of the beam.
a) The weight is to be added incrementally, meaning that the smallest person stands on the beam first, and additional weight is added until the calculated weight parameter is achieved. Record a pass or fail.
Friction test
This test will prove that the articulating parts will move back and forth with ease. Test duration should last no longer than 15 minutes.
Steps:
-
Gather all necessary supplies ( concentrically loaded steel beams from the load and fitment test, steel cable, digital scale, oil, c-clamp)
-
Lay the concentric beam so that the long edge is sitting on the table, and the welded guides labeled "4" in each diagram are closest to the table surface.
-
Attach assembly to the table with c-clamp.
-
Thread the steel cable into the front of the small beam
-
Loop the steel cable around the welded stock (label "3", small beam) located at the back of the inside beam. This is where the spring retraction device is normally located
-
Thread the steel cable out of the far out through the front end of the inside beam.
-
Tie a loop at the end of the steel cable that is now sticking out of the front of the small and larger beams
-
Power on the spring scale and pull loop from steel cable out away from the front of the beams with the scale.
-
Take several readings from 3 different positions of extension; one position where the inside beam is not extended at all, one position where the beam starts at the 1.5 foot mark as described in the load test step II, and another position approximately half the distance from the end of the beam and the mark mentioned above
-
Record and report
-
After the first trials of testing have been completed, add a light application of oil to the bottom inside of the larger beam
-
Repeat all previous steps for this test series and record/report
​
​